超(超)临界燃煤发电技术发展与展望
发布日期:2020-08-06 来源:
《热力发电》
作者:王倩 王卫良 刘敏 吕俊复 刘吉臻 岳光溪
浏览次数:188
高效燃煤发电技术一直是能源高效利用的先锋。当前主流的超(超)临界燃煤发电技术发展经历了3个阶段,技术在全球范围内逐渐成熟;在材料工业发展的支持下,朝着700 ℃等级先进超超临界技术的方向发展;并已逐步解决商业化应用的关键技术难题,迈向第4个重要发展阶段。受制于如钢材和加工等基础工业领域的薄弱条件,中国在高效燃煤发电技术研发方面长期落后于发达国家;但经过长期追赶,当前已逐渐接近世界先进水平,且在700 ℃等级先进超超临界技术研发方面,也取得了可喜成绩。在高效燃煤发电技术应用等方面,中国近四十年来发展迅猛,当前中国的煤电机组煤耗水平已达到欧洲诸国的先进水平。进一步发展材料等基础工业,从主机设备、系统布置等方面进行设计创新,仍然是高效燃煤发电技术发展的关键。
超(超)临界燃煤发电技术发展与展望
《热力发电》
王 倩1,王卫良1,2,刘 敏1,
吕俊复2,刘吉臻1,岳光溪2
(1.暨南大学能源电力研究中心,广东 珠海 519070;
2.热科学与动力工程教育部重点实验室,
清华大学能源与动力工程系,北京 100084)
[摘要]
高效燃煤发电技术一直是能源高效利用的先锋。当前主流的超(超)临界燃煤发电技术发展经历了3个阶段,技术在全球范围内逐渐成熟;在材料工业发展的支持下,朝着700 ℃等级先进超超临界技术的方向发展;并已逐步解决商业化应用的关键技术难题,迈向第4个重要发展阶段。受制于如钢材和加工等基础工业领域的薄弱条件,中国在高效燃煤发电技术研发方面长期落后于发达国家;但经过长期追赶,当前已逐渐接近世界先进水平,且在700 ℃等级先进超超临界技术研发方面,也取得了可喜成绩。在高效燃煤发电技术应用等方面,中国近四十年来发展迅猛,当前中国的煤电机组煤耗水平已达到欧洲诸国的先进水平。进一步发展材料等基础工业,从主机设备、系统布置等方面进行设计创新,仍然是高效燃煤发电技术发展的关键。
[关键词]
燃煤发电;高效;超临界;700 ℃;钢材与加工业
能源安全是关系国家经济社会发展的全局性、战略性问题。面对能源供需格局新变化、国际能源发展新趋势,保障国家能源安全,必须推动能源生产和消费革命。作为中国最主要的一次能源消费和二次能源供应者,燃煤发电的生产革命,对我国全局的能源生产革命具有决定性作用。燃煤发电的生产革命本质上就是要提高燃煤发电效率,而更高参数的超超临界发电技术无疑是高效燃煤发电技术的主要发展方向。
为了探索中国燃煤发电技术的发展道路,本文首先对当前主流的超(超)临界燃煤发电技术在世界范围内的发展脉络进行梳理;其次对当前世界上燃煤发电主要经济体的技术发展过程进行系统分析,并将中国与世界主要经济体燃煤发电产业的能耗水平进行系统比较;最后提出燃煤发电行业超超临界燃煤发电技术的主要发展方向。
1
超(超)临界发电技术发展阶段
世界上超(超)临界发电技术的发展过程大致可以分成3个阶段:
第1个阶段,从20世纪50年代开始,以美国、德国和前苏联等为代表。1949年前苏联就安装了第1台超超临界直流锅炉试验机组,机组参数为29.4 MPa/600 ℃ (12 t/h)。当时的起步参数就是超超临界参数,但随后由于电厂可靠性的问题,在经历了初期超超临界参数后,从60年代后期开始,美国超临界机组大规模发展时期所采用的参数均降低到常规超临界参数。直至80年代,美国超临界机组的参数基本稳定在这个水平。此时,美国投运超临界机组达166台,前苏联投运机组达187台。
第2个阶段,大约是从20世纪80年代初期开始。由于材料技术的发展,尤其是锅炉和汽轮机材料性能的大幅度改进,及对电厂水化学方面的认识的深入,克服了早期超临界机组所遇到的可靠性问题。同时,美国对已投运的机组进行了大规模的优化及改造,可靠性和可用率指标已经达到甚至超过了相应的亚临界机组。通过改造实践,形成了新的结构和新的设计方法,大大提高了机组的经济性、可靠性、运行灵活性。其间,美国又将超临界技术转让给日本(通用电气(GE)向东芝(Toshiba)、日立,西屋向三菱),联合进行了一系列新超临界电厂的开发设计。这样,超临界机组的市场逐步转移到了欧洲及日本,涌现出了一批新的超临界机组。
第3个阶段,大约是从20世纪90年代开始进入了新一轮的发展阶段。这也是世界上超超临界机组快速发展的阶段,即在保证机组高可靠性、高可用率的前提下采用更高的蒸汽温度和压力。其主要原因在于国际上环保要求日益严格,同时新材料的开发成功和常规超临界技术的成熟也为超超临界机组的发展提供了条件。主要以日本(三菱、东芝、日立)、欧洲(西门子、阿尔斯通)的技术为主。
截至2018年底,全世界(除中国外)已投入运行的超临界及以上参数发电机组大约有620多台。其中美国有170多台,日本和欧洲各约60台,俄罗斯及原东欧国家280余台。目前发展超超临界技术领先的国家主要是日本、德国等。世界范围内(除中国外)属于超超临界参数的机组大约有70余台。在中国,超超临界技术的应用起步较晚,但发展速度迅猛。据中国电力企业联合会(中电联)统计,2018年底中国已投产的超超临界机组已达160余台,占中国火电机组装机容量的45%,其中1 000 MW及以上机组超过100余台。中国已是世界上1 000 MW超超临界机组发展最快、数量最多、容量最大和运行性能最先进的国家。
为进一步降低能耗和减少污染物排放,改善环境,在材料工业发展的支持下,各国的超(超)临界机组都在朝着更高参数的技术方向发展。当前世界主要经济体正在开展的700 ℃等级先进超超临界技术研发过程,可以认为是超(超)临界技术发展的第4个重要阶段。
2
主要经济体燃煤发电技术发展情况
欧洲高效燃煤发电技术的发展
基于二战后比利时、法国、西德、意大利、瑞士和卢森堡等于1951年签订的《巴黎协定》,1952年欧洲煤钢联盟(ECSC)成立。受欧洲煤钢联盟的资助,欧洲于20世纪50年代开始研发适用于超超临界机组的钢材。1983年欧洲钢铁联盟在西德、英国和意大利启动91级钢铁协作研发计划,并最早应用于法国科涅(Cogne)电厂。这些工作都为超超临界机组的研制奠定基础。作为欧洲煤钢联盟的继任者,欧洲煤炭钢铁基金(RFCS)于2002年成立,进而每年资助欧洲煤炭和钢铁行业涉及安全、高效、有竞争优势的研发项目。
针对超超临界和先进超超临界(A-USC)的研发,欧洲科学技术合作组织(European Cooperation in Science and Technology,COST)计划和Joule-Thermie AD700计划启动。其中COST计划始于1971年,历经COST 50(1971年启动)、COST 501(1980—1997年,I-III期)、COST 505(1982—1986年)、COST 522(1999—2003年)和COST 536(2004—2009年)等研发项目。通过这些工作的开展,使得合金材料耐高温等特性逐步提高,从而实现燃煤/燃气机组的热效率提高10%左右。
2011年以前,欧洲投运的容量1 000 MW以上的超超临界机组为NIEDERAUSSEM-#K机组。机组容量1 025 MW,主蒸汽压力26.5 MPa,主/再热蒸汽温度576 ℃/599 ℃。此机组为德国实施火力发电深度节能优化计划(简称“BoA”计划)第1期的依托工程。在总结吸收NIEDERAUSSEM-#K机组的经验基础上,进行了进一步的改进和优化,第2期“BoA”计划的依托工程为Neurath #F、G机组,容量增加到1 100 MW,主蒸汽和再热蒸汽参数提高到600 ℃和605 ℃,电厂供电效率达到43%,污染物排放更低。同时,新建机组开始实施在现有材料基础上,主蒸汽压力进一步提高,再热蒸汽温度提升到620 ℃的方案。GE在德国卡尔斯鲁厄投运的RDK8燃煤电厂机组容量为919 MW,运行效率达到47.5%(低位热值,LHV)。另外丹麦的Nordjylland电厂3号机组虽然机组容量不大,但是采用了二次再热、深海水冷却等技术,是目前世界上机组效率最高的燃煤电厂之一。
在1997年欧洲许多国家都签订《京都议定书》的背景下,大幅减排CO2面临巨大挑战。为此,欧盟于1998年1月启动AD700先进超超临界发电计划,其主要目标是研制适用于700 ℃锅炉高温段、主蒸汽管道和汽轮机的奥氏体钢及镍基合金材料,设计先进的700 ℃超超临界锅炉及汽轮机,降低700 ℃机组的建造成本,最终建成35 MPa/705 ℃/720 ℃等级的示范电站,结合烟气余热利用、降低背压、降低管道阻力、提高综合给水温度等技术措施,使机组效率达到50%(LHV)以上。原计划通过示范电站的运行和技术完善,在2011年左右实现机组商业化运行。
AD700计划主要包括概念设计与高温材料研发(第1阶段,1998—2004年)、锅炉设计与高温材料性能测试(第2阶段,2002—2005年)、关键部件的中试实验(第3阶段,2004—2008年)、700 ℃超超临界示范电站的建设(第4阶段,2006—2011年)、示范电站的运行(第5阶段,2012—2014年)和技术反馈(第6阶段,2012—2014年)。材料部分主要通过比选市场上已有或者研发新的钢/合金材料以满足相应抗高温蠕变断裂特性。具体包括满足在100 MPa/650 ℃条件下安全运行10万h的铁素体钢、满足在100 MPa/700 ℃条件下安全运行10万h的奥氏体钢和满足在100 MPa/750 ℃条件下安全运行10万h的高温合金钢。
通过材料实验研究发现,锅炉部分涉及的昂贵的镍基合金钢(617、263和740合金)和奥氏体钢(Sanicro25)都通过了实验测试,然而所选用的几种铁素体钢材(含12%铬)在经历1万~2万h以后都存在微结构不稳定性而导致蠕变特性下降(也有报道称镍基管道在部件验证实验回路中出现了裂缝)。汽轮机部分关于阀门、高/中压转子、焊接等相关实验研究都顺利完成。其他关于锅炉、汽轮机的整体设计和具体加工制造方案和关键部件的中试实验等都已经顺利完成。
在热力系统研究过程中,丹麦DONG能源公司提出了通过在给水泵汽轮机上打孔抽汽以降低再热段(中、低压缸)回热㶲损失的MC系统。如果小汽轮机效率能提高到一定水平,可实现在同等材料基础上将机组热效率提高1.4%左右。通过与AD700原计划的方案结合,并采用海水冷却等措施,可进一步将系统热效率提高至55%。然而由于高温合金钢和奥氏体钢价格昂贵,而相对便宜等级的铁素体钢性能还没有达到预期目标,整个项目的投资会大大增加,导致本计划一再推迟。目前还没有兴建A-USC示范电厂的具体计划。
日本高效燃煤发电技术的发展
日本燃煤发电装机容量在1960年之前非常少。受20世纪70年代石油危机的影响,日本开始大规模建造燃煤机组以保障能源安全。日本大部分燃煤机组在20世纪50年代末就已从538 ℃提高到566 ℃。而到1993年以后,新建的燃煤机组一般都采用超超临界25 MPa/600 ℃/600 ℃等级的参数,机组热效率达到42%(HHV)。到2004年,日本约四分之一的电力由燃煤机组供应,其中有近一半的机组为超超临界机组。2011年福岛地震以后,几乎所有的核能发电站都被关闭,直到2015年仙台核能发电站经过政府严格审查后才重新启动。为此燃燃气发电站、燃煤电站和燃油电站等几乎全负荷工作以满足电网需求。近几年燃煤机组的发电量已占30%以上。
在超超临界技术发展成熟以后,同时也受欧洲AD700计划的影响,日本锅炉制造厂、汽轮机制造厂、阀门制造厂、研究所、高校和相关事业单位在政府支持下于2008年联合启动700 ℃ A-USC研发计划。A-USC计划的目标是在600 ℃等级超超临界技术的基础上将燃煤电站的参数提高到35 MPa/700 ℃/720 ℃/720 ℃等级(二次再热),将机组热效率提高到46%~48%(高位热值,HHV)。研发计划成立A-USC委员会,下设汽轮机、锅炉、阀门和锅炉部件测试等分委员会。
锅炉部分的工作主要包括系统设计、材料特性研究、管/板焊接、关键部件成型、抗氧化/腐蚀/疲劳/蠕变实验等研究工作。锅炉材料部分重点对镍基合金(HR6W、HR35、617合金、263合金、740合金和141合金)和铁素体钢(High-B-9Cr、Low-C-9Cr和SAVE12AD)等进行了研究。再热器、主管道、阀门和套管等都在2015—2016年通过了实炉试验。 汽轮机部分的工作主要包括系统设计、转子锻造、转子焊接与加工、阀门/内缸/喷嘴室铸造、材料的抗氧化/疲劳/蠕变等研究。
汽轮机部分重点研究了适用于700 ℃高温段的镍基(FENIX-700、LTES和TOS1X)等材料。镍基FENIX-700是在706合金的基础上减少了铌的成分,并增加了钛和铝的成分,在700 ℃下具有最好的长期稳定性。汽轮机的转子实验已于2016年在电加热试验台上完成。另外相关高温段的阀门采用如镍基材料、钨铬钴合金和表面涂层处理材料也通过了实验测试。通过上述研究发现,镍基合金、先进的9铬合金钢及其整个铸造、加工等环境是本项目的关键。
美国高效燃煤发电技术的发展
美国在超(超)临界技术的研发起步较早,目前世界上多个技术流派都源自于美国。但受国内资源禀赋等多种原因的影响,自20世纪90年代以来,美国高效燃煤发电机组的发展较为缓慢。目前美国拥有世界上单机容量最大的1 300 MW超临界双轴机组。但由于这些机组均为20世纪70年代至90年代初投入运行的,虽然单机容量为目前世界最大,其技术水平与目前世界先进的高效燃煤发电水平有较大差距。
2001年美国能源部(DOE)和俄亥俄煤炭发展办公室(OCDO)联合主要电站设备制造商、美国电力研究院(EPRI)等单位启动先进超超临界燃煤发电机组US DOE/OCDO A-USC研究项目,并成立US DOE/OCDO A-USC联盟。该项目的最终目标是开发蒸汽参数达到35 MPa/760 ℃/760 ℃的火力发电机组,效率达到45%(HHV)以上。计划到2015年,完成先进超超临界机组所涉及的材料的所有方面性能研究工作,包括长期的机械性能变化情况测试,材料微观结构发展过程的深入研究,氧化和脱落特性的研究,向火侧腐蚀特性的实炉研究,各种焊接过程和焊接性能研究,涉及转子加工过程的模具、锻造和性能测试等研究,铸造成型和表面处理等工作。
相关研究工作主要分为锅炉和汽轮机2个部分。锅炉部分从2001年启动,并于2015年全部完成。主要包括概念设计和经济性分析、高温合金的机械特性、蒸汽侧的氧化和抗氧化特性、向火侧的抗腐蚀特性、焊接性能、可加工特性、表面处理特性、设计数据和标准。汽轮机部分分为2个阶段。第1阶段从2005—2009年。主要完成方案设计和经济性分析,非焊接转子的材料研究,焊接转子的材料研究,铸造、氧化和固体颗粒侵蚀等工作。由于第1阶段完成后,阿尔斯通(Alstom)和西门子(Siemens)终止参与,所以第2阶段从2010年开始又根据第1阶段研究的优选材料针对GE开发的螺栓连接的转子开展相关性能研究。第2阶段的具体研究内容包括转子/压力盘测试(全尺寸锻造成型和示范)、叶片和螺栓的长时间测试、汽轮机缸体和阀体的铸造、套管焊接和铸造修复等工作。上述工作已全部于2015年完成。
通过上述研究,US DOE/OCDO A-USC联盟完成了先进超超临界电厂基于镍基合金的焊接和制造相关示范工作,完成了基于世界上第1台760 ℃汽冷腐蚀测试实验系统的高温合金材料向火侧腐蚀特性实炉研究,完成了高温时效硬化合金、用于锻造转子的新型材料的铸造技术研发,以及作为核心材料的耐760 ℃电厂用铬镍铁合金740H的验收标准。基于上述14年研发工作的顺利开展,目前美国US DOE/OCDO A-USC联盟正在开展相关关键部件实验平台的建造工作。
中国高效燃煤发电技术的发展
中国从1992年开始兴建超临界机组,直到21世纪初才开始引进超临界/超超临界技术。2004年首台国产超临界机组投产后,国家科技部又将“超超临界燃煤发电技术”列入“十五”863项目,极大促进了我国600 ℃/600 ℃一次再热超超临界机组的引进和消化吸收。国内主机厂通过不同的合作方式引进、消化并吸收国外技术,逐步实现了超超临界机组的国产化。
最初东方电气集团、哈电集团现有超超临界机组汽轮机进口参数为25 MPa、600 ℃/600 ℃,相应锅炉的设计参数为26.25 MPa、605 ℃/603 ℃。上海电气集团超超临界机组汽轮机进口参数选用26.25~27 MPa、600 ℃/600 ℃的方案,相配套的锅炉其主蒸汽压力约27.5~28.35 MPa。在引进消化、吸收以后,三大制造厂在新项目中逐步开展了优化设计研究,比如将主蒸汽压力从25 MPa逐步提高到28、31 MPa,将再热蒸汽温度从600 ℃逐步提高到615、620 ℃等。如浙江长兴电厂2014年投产的660 MW超超临界机组将主蒸汽参数提高到28 MPa/600 ℃/620 ℃,泰州电厂2015年投产的1 000 MW超超临界二次再热机组将主蒸汽参数提高到31 MPa/600 ℃/610 ℃/610 ℃,发电效率已达到47.8%。
目前中国已是世界上1 000 MW超超临界机组发展最快、数量最多、容量最大和运行性能最先进的国家。我国25~31 MPa/600 ℃等级超超临界发电技术已经逐步成熟,同时具备了630 ℃超超临界机组的研发能力。大唐郓城35 MPa/615 ℃/630 ℃/630 ℃超超临界二次再热国家电力示范项目已于2019年获批。目前正在开展630~650 ℃材料的研制和开发,建设630~650 ℃机组已成为下一步电站建设的重要目标。
我国超临界和超超临界发电技术比发达国家起步晚,但利用国内市场提供的巨大舞台,通过前期的技术转让以及后期的自主研发,目前具有先进水平的设计制造平台、全球600 ℃超超临界机组最多的设计运行经验,为我国700 ℃超超临界燃煤发电技术的发展奠定了良好的基础。为此,我国从2010年7月23日在北京成立“国家700 ℃超超临界燃煤发电技术创新联盟”,其组成单位包括五大发电集团、三大动力集团,以及重点电力设计和研究单位、材料研究和冶炼单位等。2011年6月24日国家能源局在北京组织召开了国家700 ℃超超临界燃煤发电技术创新联盟第1次理事会议和技术委员会会议,正式启动700 ℃超超临界燃煤发电技术研发计划的工作。根据700 ℃高效超超临界发电技术的难点及与国外差距,我国初步确定700 ℃计划示范机组容量采用600 MW等级,压力和温度参数为35 MPa/700 ℃/720 ℃,机组采用紧凑型布置,再热方式按照一次再热和二次再热2种方案开展研究,并制定了初步研发进度。原计划在“十二五”末建立660 MW,35 MPa/700 ℃/720 ℃的示范电站,但由于耐高温材料等研制的影响,项目进度一再推迟,目前尚未获悉该示范机组建设的具体进展。
根据700 ℃超超临界燃煤发电技术的目标要求,国家能源局设立了“700 ℃超超临界燃煤发电关键设备研发及应用示范”重点研发项目。该项目内容主要包括机组总体方案设计研究、关键材料技术研究、锅炉关键技术研究、汽轮机关键技术研究、关键部件验证试验平台的建立及运行、示范电站建设的工程可行性研究等6个方面。从2012年开始,中国钢铁研究院、抚顺特殊钢厂、内蒙古重工、宝钢、中国一重、中国二重、中科院金属所等联合开发700 ℃超超临界燃煤发电技术所需的耐高温材料。同时还引进了740H、617B、Sanicro25、Haynes282、Nimonic80A等镍基或铁镍基高温合金材料,并组织西安热工研究院、上海成套院、哈尔滨锅炉厂等单位对其成分、力学及持久性能等开展详细分析。目前,我国宝钢集团、太钢集团等冶金/制造企业已试制出了镍基高温材料的管材。中科院金属研究所通过对984合金改进得到984G合金。宝钢集团也试制出了984G管材,并正在进行相关性能试验。华能清能院联合东锅和西北电力设计院,完成了700 ℃紧凑型超超临界煤粉锅炉的初步设计。依托南京电厂的700 ℃实炉超超临界燃煤发电机组关键部件验证实验平台于2015年底建成投运,并2017年10月通过专家鉴定。2018年2月科技部对“863”计划项目“700 ℃超超临界发电关键技术研究”进行了验收,提出了一套自主设计的700 ℃超超临界锅炉、汽轮机、高温蒸汽管道系统的关键部件选材方案,为进一步开展700 ℃等级高效超超临界发电关键技术的研究奠定了良好的基础。
材料和制造技术是发展先进机组的技术核心,而我国的高温材料基础研究薄弱。自主产权高温材料数据库的缺乏,成为制约700 ℃超超临界发电技术的瓶颈。目前国内外700 ℃材料都不太成熟,而且价格及其昂贵。从主机设备、系统布置等方面进行设计创新,努力减少高温材料的使用,降低工程投资,是目前全世界共同研究的方向之一。
3
世界主要国家燃煤机组发电煤耗对比分析
在电力行业,燃煤机组发电煤耗每下降10 g/(kW‧h),意味着技术领先一个时代。根据国际能源署(IEA)提供的燃煤机组煤炭消耗及发电量,选取中国、美国、澳大利亚、日本、韩国、印度、法国、德国、北欧(丹麦、瑞典、芬兰、挪威)、英国和爱尔兰等世界主要国家和地区的相关数据,并参考日本MRI研究协会分析报告所提出的方法计算了各个国家燃煤机组的发电效率,整理得到上述国家燃煤机组的煤耗情况。考虑到有些地区的电网交叉性很强,难以分割,如北欧四国地区,以及英国和爱尔兰地区,本文分别将这些地区合并讨论。并对所选择国家的煤耗情况进行直接代数平均和加权平均(即总量平均)作为2个参考指标。根据IEA的统计数据(官网更新至2017年),本文所选择的14个国家化石燃料的发电量占全世界化石燃料发电量的66%左右,具有较强的代表性。另外,由于缺乏各个国家燃煤机组厂用电率的统计数据,本节主要对比的是发电煤耗的情况。
由于欧洲燃煤技术发展总体水平较高,为了方便讨论,将中国燃煤发电的煤耗情况与欧洲主要国家和欧洲以外主要国家分别进行对比分析。图1为中国与美国、澳大利亚、日本、韩国和印度等非欧洲主要国家平均发电煤耗的对比情况。
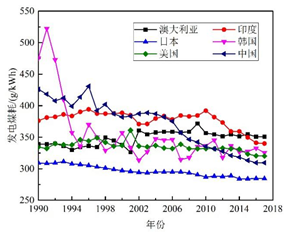
(图1 中国与美国、澳大利亚、日本、韩国和印度等非欧洲主要国家平均发电煤耗比较)
从图1可以看出:
1)中国在20世纪90年代燃煤机组发电煤耗水平总体落后,只比韩国的低。但由于韩国当时装机容量基数很小(年耗煤量只有600万t,仅相当于中国的4%,IEA数据),受当时韩国经济发展需求的拉动,1995年比1990年新增装机容量1.8倍左右(根据IEA提供燃煤发电消耗量和总效率估算)。大量高效新机组的投运推动了燃煤机组整体效率的大幅提高,发电煤耗从1990、1991年的500 g/(kW‧h)左右飞速降低至1995年的335 g/(kW‧h)。以至于中国从1993年开始成为图1中煤耗最高的国家。
2)自1995年以来中国发电煤耗总体上持续稳定下降(图中的几个波动点疑似统计出入),分别在2006年后开始明显低于印度,在2007年后开始明显低于澳大利亚,在2011年后明显低于美国,与韩国相近。虽然自2010年以后印度燃煤机组的发电煤耗也开始稳定持续下降,但与中国仍有较大差距。然而,由于日本自20世纪80年代以后,燃煤机组已全部更新为超临界机组,因而燃煤机组总体煤耗水平较低。自1993年以后日本开始大力发展大容量超超临界机组(同时也建造了少量增压流化床联合循环亚临界机组),使得日本燃煤机组的发电煤耗开始进一步稳定下降。虽然总体下降幅度不大,但由于其早期煤耗水平较低(1993年为311 g/(kW‧h)),一直保持着世界领先的地位。截至2017年,日本燃煤机组的平均发电煤耗已经下降至284 g/(kW‧h)。
3)美国和澳大利亚等国家自20世纪90年代以来几乎没有新建火力发电机组。其中澳大利亚总体电力工业除了在可再生能源领域有所增长之外,总体电力装机增长很小;而美国自2000年以后的电力增长点主要集中在燃气机组方面,从而导致这2个国家的发电煤耗水平基本维持不变,甚至澳大利亚燃煤机组因老化而导致煤耗一定程度升高。
图2为中国与欧洲主要国家燃煤机组发电煤耗的对比情况。
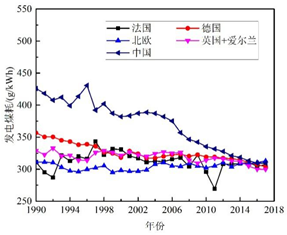
(图2 中国与欧洲主要国家燃煤机组发电煤耗的比较)
从图2可以看出:
1)欧洲各国的发电煤耗总体较低。虽然德国在1990年发电煤耗相对较高,但经过20世纪90年代开展的一些列深度节能降耗措施,如燃煤锅炉余热利用提效的“BoA”计划等,使得德国燃煤机组的煤耗水平在装机容量没有明显增加的情况下发电煤耗从356 g/(kW‧h)大幅降低至318 g/(kW‧h)左右。但由于燃煤机组的节能潜力已经挖掘完,且又没有大量新建先进机组拉动,导致其发电煤耗近十几年来没有明显变化。欧洲其他几个国家由于燃煤机组近二十多年都没有明显变化,因而其发电煤耗也一直维持平稳。其中法国燃煤机组容量太小(1 GW量级),容易受负荷率、机组更新等变化影响波动较大。而北欧的装机容量也只有法国的2倍左右,其煤耗总体最低。
2)中国的发电煤耗水平与欧洲国家相比长期处于大幅落后状态。在2007年以后由于大量小机组的关停,导致煤耗直线下降。又随着近几年煤耗的稳步下降,到2017年已经与欧洲总体相当。
图3为中国发电煤耗与所选的10个国家和地区发电煤耗平均水平的比较情况。其中选取国家代数平均为基于IEA数据选取的美国、澳大利亚、中国、日本、韩国、印度、英国和爱尔兰地区、法国、德国、北欧四国地区等14个国家和地区燃煤机组发电煤耗数据的代数平均情况,其主要反映了世界各国的技术水平分布情况,但不能反映世界燃煤发电的总体煤耗情况。而选取国家的加权平均考虑了各个国家燃煤发电量的权重,但易受如中国、美国等能源消耗大国的主导,从而难以体现日本等先进国家对总体的影响。其中中国-IEA数据与其他国家的数据都是基于IEA提供能源平衡数据整理而得,而中国-中电联数据是根据中电联发布的历年电力工业快报统计而出。从图3中可以发现,中电联的统计数据与基于IEA数据整理的结果有较大误差,但总体趋势越来越接近,其中2017年的误差约14 g/(kW‧h)。结合项目组到国内各家电厂调研的情况,综合认为中电联统计的数据存在10 g/(kW‧h)以上的水分。而IEA的数据则可能因口径统计偏差会存在一定的误差,但总体上更为可靠。
先统一采用IEA的数据来源,将中国与所选取国家和地区发电煤耗的加权平均情况相比较。可以看出,在20世纪90年代,中国燃煤工业的发电煤耗水平与世界平均水平差距较大,相差约70 g/(kW·h)。随着中国电力工业近三十年的飞速发展,燃煤工业的发电煤耗逐渐下降,也与世界所选国家和地区加权平均水平逐渐减小。特别是通过“十一五”期间大规模关停小火力发电机组,并新建大量大容量、高参数的高效燃煤机组,2010年中国燃煤工业的发电煤耗已经开始低于世界加权平均水平。
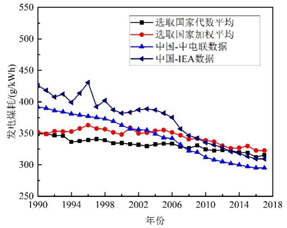
对比世界所选国家和地区燃煤机组发电煤耗的加权平均与代数平均的情况可以看出,在20世纪90年代时二者并无明显差别,但随着中国、印度等国家装机容量的大幅增长,而其他发电煤耗较低的国家装机容量总体增长不明显,导致发电煤耗的加权平均值受中国、印度煤耗较高的影响越来越明显,高于代数平均值,在1995—2005年期间长期高20 g/(kW·h)左右。然而,随着中国发电煤耗水平的大幅下降,所选国家燃煤机组发电煤耗的加权平均与代数平均差距在2005年以后越来越小。直至2013年,中国燃煤机组的发电煤耗开展降低至所选国家燃煤机组发电煤耗的加权平均水平,中国燃煤机组的发电煤耗水平开始对世界燃煤机组发电煤耗的加权平均值进行反向拉动。预期再过几年,选取国家燃煤机组发电煤耗加权平均水平有可能受中国发电煤耗持续下降的影响低于代数平均值。
根据IEA数据,2017年全世界发电量共约25 721 TW·h,其中燃煤机组的发电量约占38%,约9 863 TW·h。而2017年中国燃煤机组的发电量就达4 509 TW·h,约占全世界燃煤机组发电量的46%。中国燃煤机组的节能降耗情况直接影响全世界燃煤机组的总体能耗水平。根据中国燃煤机组发电煤耗水平与所选时间各国的对比情况来看,中国燃煤机组的发电煤耗已经达到世界平均水平,明显低于澳大利亚、印度等相对落后的国家,与欧洲主要国家接近,与日本等领先水平还存在25 g/(kW·h)左右的差距(2017年水平)。总体上看,中国燃煤机组的煤耗水平还有一定的下降空间。
4
结论与展望
1)总体上看,美国是超(超)临界技术发展最早的国家,但是受资源结构的影响,美国燃煤发电装机发展较为缓慢,且能耗水平早已被诸多国家赶超,但其超超临界燃煤发电技术却一直保持着世界领先水平。欧洲在超(超)临界技术发展上同样起步较早,基础雄厚,且是700 ℃等级超超临界技术的最早提出与践行者;许多燃煤发电机组先进的节能理念都源自于欧洲,其煤耗水平一直处于世界先进行列。日本在19世纪80年代继承了美国先进的技术后,开展了燃煤发电机组的全面升级,其发电煤耗水平很快领跑国际;其先进700 ℃等级超超临界技术虽然起步较晚,但发展迅速,已顺利完成关键技术开发,制造能力上已达到与美、欧三分天下的水平。中国的电力工业发展虽然不晚,但受近百年来的世界格局影响,整体工业水平长期落后于发达国家。超(超)临界技术的早期发展也主要依赖于引进国外技术及关键材料。然而,近四十年来,受我国整体经济高速发展的刺激,电力工业一直是我国工业发展的先锋,装机容量发展迅速,发电煤耗长期持续大幅下降,电力工业整体运行状况已达到世界先进水平。
2)国家能源局“十四五”电力规划启动会指出,加速电力绿色转型升级,重点在推动煤电清洁高效发展。提高机组参数是促进超超临界燃煤发电技术高效化的主要举措。目前,中国是全球最大的已安装发电基地,正在开展700 ℃等级先进超(超)临界技术研发。尽管示范机组建设项目已被推迟,但是提高蒸汽参数的技术研究仍在进行中。受材料、加工制造等基础工业的影响,高温材料仍然是制约超超临界燃煤发电技术发展的瓶颈。因此,从主机设备、系统布置等方面进行设计创新,努力减少高温材料的使用,降低工程投资,是目前中国乃至全世界的研究方向之一。
3)超超临界燃煤发电技术和其他技术耦合也是未来发展方向之一。四川白马电厂600 MW超临界循环流化床(USC-CFB)示范工程已投入商业运行,是世界上容量最大的USC-CFB锅炉,处于世界领先行列。耦合生物质、垃圾发电技术与超超临界燃煤发电技术,有望成为规模化清洁高效利用低热值、劣质燃料发电的主要技术手段。
4)整体而言,我国的燃煤发电技术与美、日、欧等世界先进水平还有较大差距。推动我国基础工业的发展已成为我国电力工业进一步发展的瓶颈,也是整个工业发展的瓶颈,应作为我国经济发展战略的重中之重。
[引用本文格式]
王 倩, 王卫良, 刘 敏, 等. 超(超)临界燃煤发电技术发展与展望[J]. 热力发电, 2020, 49(预出版): 1-9. [doi:10.19666/j.rlfd.202007179].
WANG Qian, WANG Weiliang, LIU Min, et al. Development and prospect of ultra-super critical coal-fired power generation technology[J]. Thermal Power Generation, 2020, 49(预出版): 1-9. [doi:10.19666/j.rlfd.202007179].